Discover What is Porosity in Welding and Its Impact on Architectural Honesty
Discover What is Porosity in Welding and Its Impact on Architectural Honesty
Blog Article
The Science Behind Porosity: A Comprehensive Guide for Welders and Fabricators
Understanding the complex mechanisms behind porosity in welding is vital for welders and fabricators making every effort for remarkable craftsmanship. As metalworkers look into the midsts of this phenomenon, they reveal a globe controlled by different aspects that affect the formation of these small voids within welds. From the composition of the base products to the intricacies of the welding process itself, a plethora of variables conspire to either intensify or reduce the visibility of porosity. In this comprehensive guide, we will certainly untangle the scientific research behind porosity, discovering its results on weld top quality and introduction advanced strategies for its control. Join us on this journey via the microcosm of welding blemishes, where accuracy satisfies understanding in the pursuit of flawless welds.
Understanding Porosity in Welding
FIRST SENTENCE:
Examination of porosity in welding reveals vital insights into the honesty and top quality of the weld joint. Porosity, identified by the presence of dental caries or spaces within the weld steel, is a typical concern in welding procedures. These gaps, if not effectively resolved, can compromise the structural honesty and mechanical buildings of the weld, resulting in prospective failings in the completed product.
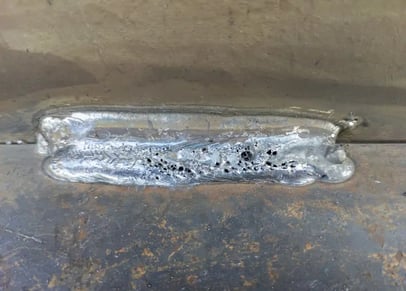
To find and measure porosity, non-destructive testing methods such as ultrasonic testing or X-ray inspection are typically utilized. These strategies permit the identification of inner flaws without endangering the integrity of the weld. By examining the dimension, shape, and distribution of porosity within a weld, welders can make enlightened choices to improve their welding processes and accomplish sounder weld joints.

Variables Affecting Porosity Formation
The occurrence of porosity in welding is influenced by a myriad of factors, ranging from gas securing effectiveness to the details of welding criterion settings. Welding specifications, including voltage, present, take a trip speed, and electrode kind, likewise influence porosity development. The welding technique employed, such as gas metal arc welding (GMAW) or shielded steel arc welding (SMAW), can affect porosity formation due to variants in warm circulation and gas protection - What is Porosity.
Effects of Porosity on Weld High Quality
Porosity formation considerably jeopardizes the architectural honesty and mechanical buildings of welded joints. When porosity is existing in a weld, it creates gaps or dental caries within the product, minimizing the general toughness of the joint. These spaces act as stress and anxiety concentration factors, making the weld a lot more at risk to cracking and failing under lots. The presence of porosity likewise weakens the weld's resistance to corrosion, as the caught air or gases within deep spaces can react with the surrounding setting, resulting in deterioration in time. In addition, porosity can impede the weld's capacity to endure stress or influence, more endangering the general top quality and dependability of the bonded framework. In crucial applications such as aerospace, automotive, or structural constructions, where safety and security and resilience are extremely important, the damaging impacts find out here now of porosity on weld quality can have severe repercussions, highlighting the importance of minimizing porosity via appropriate welding strategies and procedures.
Strategies to Minimize Porosity
Additionally, using the suitable welding parameters, such as the correct voltage, current, and travel speed, is important in avoiding porosity. Maintaining a regular arc length and angle throughout welding additionally helps minimize the possibility of porosity.

In addition, choosing the ideal protecting More hints gas and keeping appropriate gas circulation prices are necessary in decreasing porosity. Making use of the suitable welding technique, such as back-stepping or employing a weaving activity, can additionally aid distribute heat evenly and minimize the opportunities of porosity formation. Lastly, guaranteeing proper air flow in the welding environment to eliminate any type of potential resources of contamination is crucial for achieving porosity-free welds. By carrying out these strategies, welders can efficiently lessen porosity and create high-grade bonded joints.
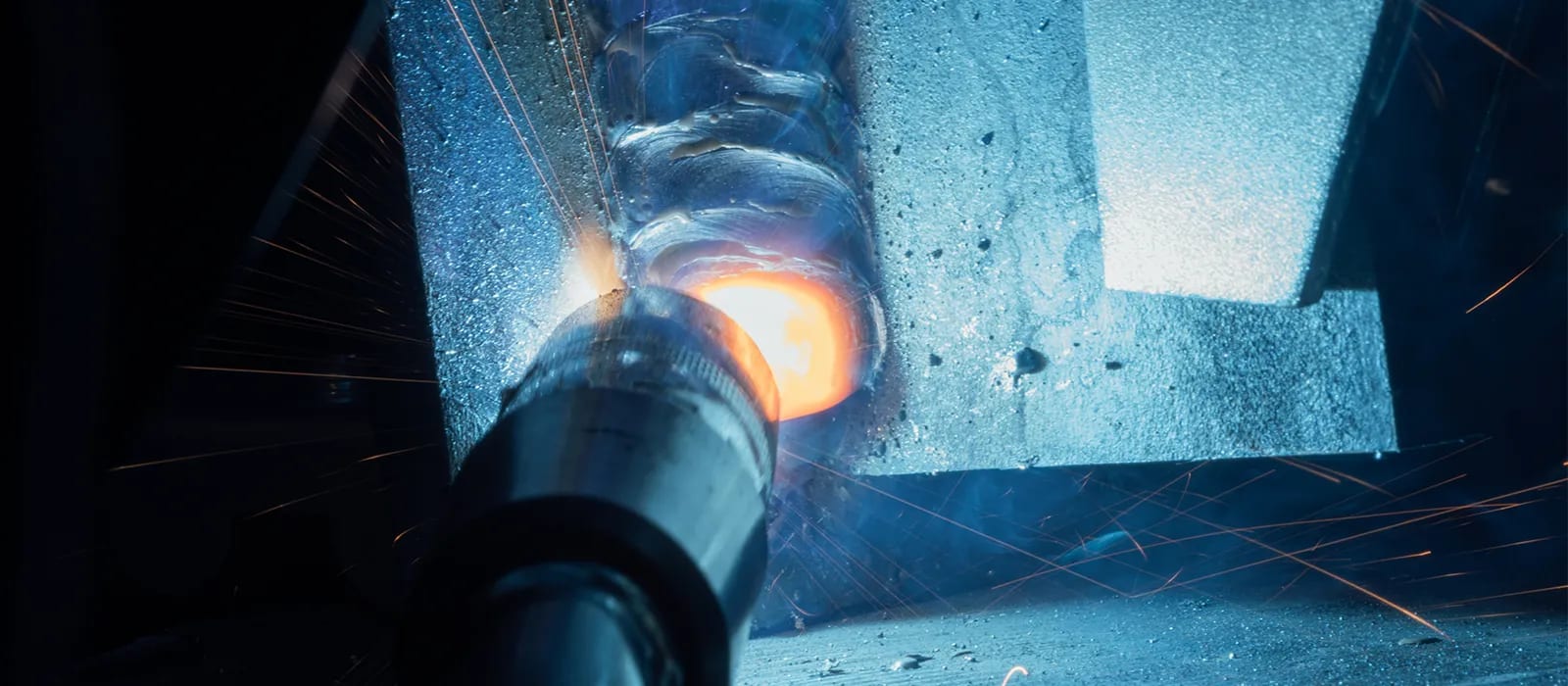
Advanced Solutions for Porosity Control
Executing innovative technologies and ingenious approaches plays an essential role in attaining exceptional control over porosity in welding procedures. In addition, utilizing advanced welding techniques such as pulsed MIG welding or modified environment welding can additionally aid alleviate porosity concerns.
One more sophisticated service involves the use of advanced welding tools. Making use of tools with integrated features like waveform control and sophisticated power sources can boost weld quality and decrease porosity dangers. The execution of automated welding systems with specific control over specifications can considerably minimize porosity flaws.
Additionally, incorporating advanced tracking and inspection technologies such as real-time X-ray imaging or automated ultrasonic testing can aid in discovering porosity early in the welding procedure, enabling for instant rehabilitative actions. On the whole, incorporating these innovative services can substantially boost porosity control and enhance the overall high quality of welded elements.
Final Thought
In verdict, understanding the science behind porosity in welding is crucial for welders and producers to create top quality welds. By determining the aspects affecting porosity formation and executing methods to More Info reduce it, welders can improve the general weld quality. Advanced solutions for porosity control can even more improve the welding procedure and make certain a strong and reliable weld. It is essential for welders to continuously inform themselves on porosity and apply finest methods to achieve ideal outcomes.
Report this page